- By
- Posted Thursday, January 30, 2020 - 11:45
BridgeComposites, LLC of Hornell, NY uses a LORD MicroStrain wireless bridge monitoring system to evaluate seismic isolation bearings.
Wireless Systems and Smart Bridges
Unique traffic loads, environmental conditions and seismic events can exert undesirable stresses on structures such as highway bridges. One in four of bridges in the Unites States are either structurally deficient or functionally obsolete.
BridgeComposites, LLC of Hornell, NY uses a LORD MicroStrain wireless bridge monitoring system to evaluate seismic isolation bearings. A network of low-power wireless sensor nodes supply continuous synchronized performance and environmental data to engineers in real-time. Remote, cloud-based data visualization and analytic tools on MicroStrain’s SensorCloud™ enable BridgeComposites and researchers to more efficiently and cost-effectively characterize the long-term performance of bridge components.
Scalable Networks and Rapid Installations
Quantifying bridge performance requires a distributed network of monitoring capabilities. However, installing conventional hardwired solutions pose numerous cost, labor and logistical barriers to achieve adequate scale. LORD MicroStrain’s wireless solution drastically reduces time and disruption associated with hardwired installations, while preserving synchronized high-speed data across any length bridge.
In a matter of hours, a team of two engineers fully deployed the wireless bridge monitoring network. The network was comprised of seven wireless sensor nodes including: two G-Link® acceleration nodes, two DVRT® linear displacement transducers, two TC-Link® temperature nodes, and an SG-Link® strain node. Lossless, extended range, synchronized sampling ensured reliable data communication in the ferrous environment. Advanced energy management protocols and energy harvesting capabilities promise multi-year operation without battery replacement.
Each sensor records a specific measurement that captures the in-service behavior of the bearings. Accelerometers continuously sample bridge vibration at 16Hz. Collected data allows researchers to determine the ability of new bearings to accommodate normal stresses but also to prevent damage from potential ground motion. Linear motion sensors installed on two different bearings measure the longitudinal movement of the bridge through thermal cycles. A strain gauge was mounted to an end diaphragm beam to measure forces that might be experienced during a seismic event.
Unlimited Bridge Performance Data on SensorCloud™
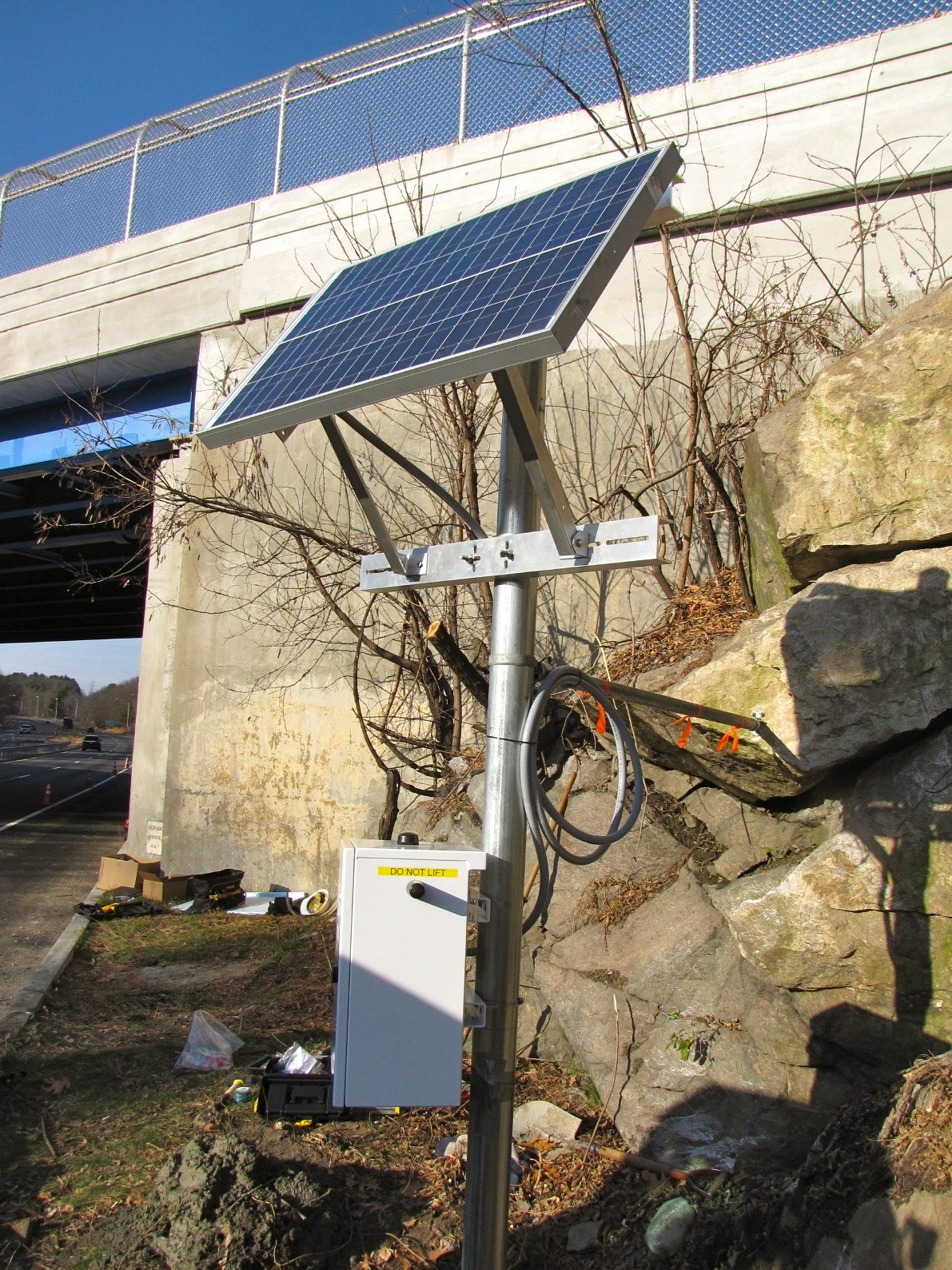
LORD MicroStrain’s web-enabled WSDA®-1000 gateway aggregated time-
stamped data at user configurable rates from across the network. Data was communicated via cellular modem to, SensorCloud™ where BridgeComposites could view and share data with the bridge owner and collaborators. Furthermore, users can create threshold alerts that automatically send email or text notifications when a pre-determined condition is exceeded.
According to BridgeComposites President, Jerome O’Connor, "While the system records data under an infrequent extreme events such as an earthquake, BridgeComposites is also able to quantitatively assess bearing performance remotely in real-time. Specifically, capturing the bearings behavior under traffic loading and changing environmental conditions enabled our engineers to observe response under actual service conditions."