Vehicle Navigation and Tracking
MicroStrain's cost-effective IMU, AHRS and GNSS/INS sensors are a trusted product in Unmanned Aerial Vehicles (UAVs), Unmanned Ground Vehicles (UGVs), and Drone navigation and tracking. Our miniature, lightweight sensors can be deployed in a variety of defense and commercial autonomous platforms to improve the accuracy and reliability of navigation and tracking.
With industry-leading size, weight, and power consumption, MicroStrain inertial sensors offer an optimal solution for unmanned land, sea and air vehicles to achieve excellent inertial sensing, vehicle tracking, and antenna pointing performance. All of our sensor systems are factory-calibrated over their full operating temperature range to ensure highly reliable performance between devices.
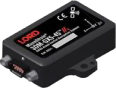
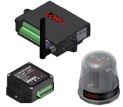
Ian Moore, Field Application Engineer
The new 3DM-GQ7-GNSS/INS builds on the success of the 3DMGX5-GNSS/INS and adds many features desired by customers which resolve common challenges in specific use cases. This test report highlights four evolutionary improvements.
Asa Davis, Zach Fuchs, Erin Gunn, Rachel Masters, Christopher Robertson, Benjamin Say, David Schenkenberger
Drones already have their own internal IMU's, but those IMU's lack the accuracy needed for larger flight tasks. For shorter flights and recreational flying, the internal IMU is precise enough to keep the drone running as expected. A
The GV7 series of inertial sensors offers improved performance and functionality over the GX5 series while maintaining the same compact size and easy-to-replace design. This upgrade is ideal for those seeking higher accuracy and additional features.
Joel John, Software Engineer
By leveraging the strengths of both radar and INS, engineers and researchers can develop more capable and adaptable autonomous robots for a variety of applications, from industrial automation to autonomous vehicles.
Technology evolves as we improve how information is gathered, analyzed and implemented into various applications. For instance, Vertical Takeoff and Landing aircraft (-VTOL) can take off, hover and land vertically.
Aidan Laracy, Field Applications Engineer
Our Field Applications Engineer, Aidan Laracy, did a deep dive to compare the performance of NMEA and MIP GNSS data input methods for the 3DM-CV7-INS. Learn as he explores the trade-offs between ease of integration and precision.
Developing humanoid robots involves an intricate blend of disciplines, including mechanical engineering, electronics, computer science, and artificial intelligence. THEMIS stands as a testament to these complex challenges.
Thiago A. Rodrigues, Jay Patrikar, Bastian Wagner, Sebastian Scherer, Constantine Samaras
Parker LORD sponsors research to model energy consumption for quadcopter package delivery drones
Ian Moore, Field Application Engineer
This report compares the steps necessary to use magnetometer vs dual-antenna as a heading source for a Cessna 150M flown in a repeated flight profile.
John Bergstrom
A case study of the GQ7 with dual antenna and RTK modem to collect navigation and position data using SensorConnect Software
Parker MicroStrain 2020
MicroStrain’s miniature, lightweight inertial navigation solutions improve navigational accuracy while reducing power consumption in next-generation unmanned ground vehicles (UGV).
Parker Hannifin MicroStrain
Underwater Remotely Operated Vehicles (ROVs) and Unmanned Underwater Vehicles (UUVs) operate in extremely demanding environments that require precise and reliable feedback. Inertial navigation solutions must be very accurate...
ParkerHannifin MicroStrain
MicroStrain inertial sensors help Team Explorer, from Carnegie Mellon and Oregon State University win the first 2019 DARPA challenge event. with both aerial and ground robots.
MicroStrain
MicroStrain® provides high-performance inertial sensing systems with minimal weight,size, and integration barriers
Parker MicroStrain
D. O'Neil, MicroStrain; S. Low, Boeing Military Aircraft Corp.
Immediate data feedback allowed flight engineers to make critical adjustments shortly after each test, enabling multiple tests per day. Previous test programs required week-long delays between flights for data analysis.
Dan O'Neil, Steve Low
Aircraft flight test has traditionally been expensive and time consuming to accomplish, requiring complex hardware design and integration and extensive operational test teams to address aircraft downtime for instrumentation maintenance and calibration,